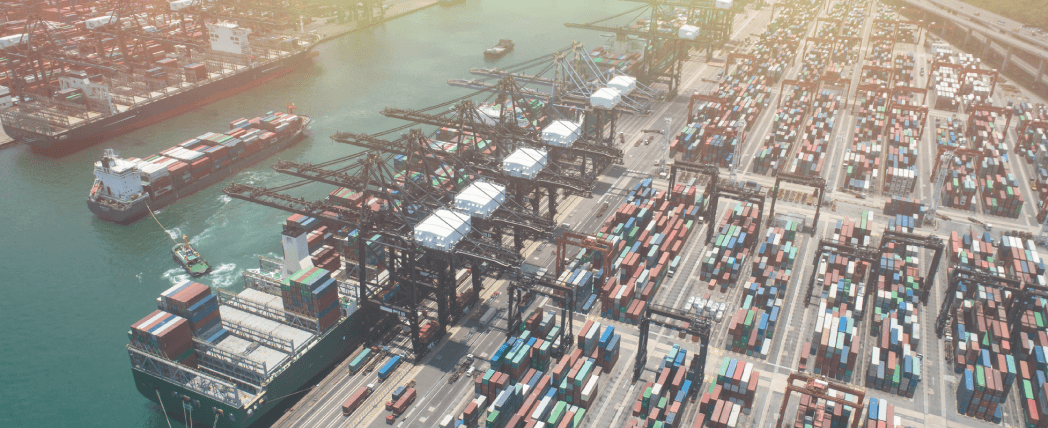
The Story at a Glance
- COVID-19 has driven a confluence of supply chain phenomena, ranging from reduced labour and raw material availability to complex shipping delays and increased demand for electronic devices for the home office. These impacts have led to major supply chain disruption globally.
- This perfect storm of events has driven historically high shipping costs as well as rising material costs. As a result, manufacturers are having to raise prices, leading to accelerating inflation in the general market.
- Just in time availability of product is over! AV professionals now need to work smarter and plan inventory better to secure the best prices and get the stock they need to win and lock in profitable projects.
- Distributors can add value to customers by ensuring a good working knowledge of possible product substitutes that keep the supply wheels turning.
Our Current Context
“Worldwide shipping is in crisis, caused partly by the pandemic. The network of ports, container vessels and trucking companies that moves goods is tangled – and the cost of shipping is skyrocketing. Fixing the problem is going to take considerable time.” – Jas Kalra, Assistant Professor in Supply Chain Management at Newcastle University.(1)
We have seen significant supply disruption as a result of COVID-19. Initially, the forecasted constriction of demand and market activities caused a plunge in orders. Factories adjusted by lowering expectations and workforces, resulting in a lowering of production capacity. However, demand for consumer electronics then actually rose with the lockdowns, as working from home professionals around the world upgraded everything from laptops, home office monitors and webcams to new Wi-Fi routers, to facilitate content streaming on their new 4K televisions. This subsequent and unexpected boom in demand for consumer electronics left factories in the lurch, unable to meet this increased demand.
By far the biggest pain point in 2021 for AV professionals and manufacturers alike has been the disruptions to shipping, with increased schedule volatility and costs, as shippers compete for containers and capacity. Container shortages, overbooked air cargo space, and booming demand has increased shipping costs two to three-fold since the beginning of the year.
As a result of delayed shipping schedules and tighter supply, delays to product availability are now an increasingly normal occurrence.
For the AV professional:
- Demand is high for product
- Manufacturing components are in low supply
- Shipping is difficult, expensive and not expected to change in the near future
“Shifting manufacturing is much more complicated than a train on tracks. We are a long way from streamlining supply. And just like it takes a long time to stretch a 150 container cargo train before it can move forward or stop, imagine having to turn it around on a dime?”
– James Chen, Kordz Managing Director
The Manufacturing Situation in China
The world’s factory is still, for all intents and purposes, China. Due to the disruptions caused by COVID-19, factory activity within China ramped up towards the latter half of 2020 in order to meet rising global demand in many consumer products. This has led to systemic imbalances in supply and demand on various levels.
Increased demand on consumer goods means an increased demand of raw materials, such as wood pulp or copper, much of which China imports from other countries still affected by COVID-19 outbreaks. The resulting supply shortages, exacerbated by the congested logistics market, has led to material cost inflation that was passed onto brands and consumers throughout 2021.
The current power shortages in many of China’s manufacturing hubs is the product of imbalances in the electricity market. An increase in power consumption due to increased factory activities has led to shortages in the coal supply, as the majority of China’s power is fuelled by coal. Consequently, the price of coal has increased. However, as power prices are regulated by the government, power stations have opted to cease operations, rather than run at a loss, thereby sparking power rationing with some heavy industries only being allowed operations one day per week. As a result of these market forces, China is shifting strategies and ensuring coal supply stability, which will still take some time. In the meantime, the effects of power rationing are being felt through further manufacturing delays.
Global Logistics
Port Congestions
As COVID-19 case counts increased throughout 2020 and 2021, the availability of dockworkers and truckers in the logistics supply chain dwindled, which in turn led to a reduction of throughput capacity at the docks. At the same time, the demand for goods – particularly those that utilise the same components found in AV products – did not subside as first predicted. As a result, port congestion worsened, with demand outstripping capacity. At the time of writing an estimated 100 or so vessels are waiting outside Hong Kong / Shenzhen ports and 35 or so outside Los Angeles / Long Beach ports, according to Bloomberg’s Port Congestion Monitor.
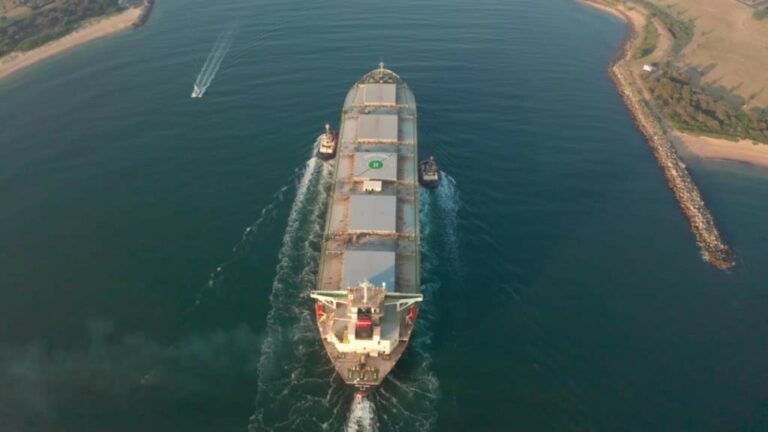
Given the already tight logistics market, disruptions such as the Suez Canal blockage in March 2021 or, more recently, typhoons in Shanghai and Hong Kong, have magnified these effects. It is important to note that while disruptions may only last a few days, the ongoing ripple effects often last many weeks thereafter. Furthermore, due to the interlinked nature of global logistics, delays and congestion in one area of the world today often means port congestions in another area of the world tomorrow. As a result, shipping rates have soared as the competition for containers and carriage intensifies, evidenced by the 500%+ rise in 40-foot container costs over the course of the pandemic(3), according to Drewry, a maritime and supply chain research firm.
The Shortage of Shipping Containers
While ships are waiting outside of ports around the world, so too are the containers on board those ships, leading to a global shortage of containers. With an average ship holding anywhere between 10,000 Twenty-foot Equivalent Unit (TEU) to 21,000 TEUs, this equates to anywhere between 350,000 – 735,000 containers in limbo outside the west coast of the United States alone, and more than quadruple that in Asia’s major ports (Hong Kong, Shanghai and Singapore).
“The average price for a standard 40-foot Chinese made shipping container this year is more than double what it was in 2016.”
– Jas Kalra, Assistant Professor in Supply Chain Management at Newcastle University(1)
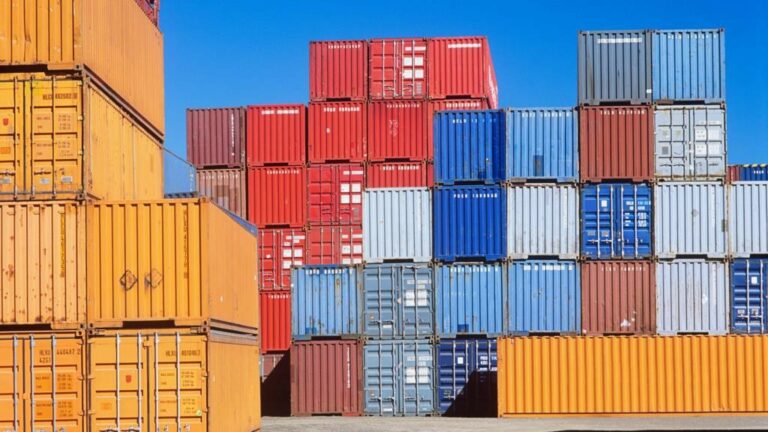
The competition for empty containers at export countries have intensified to the point that most shipping companies are now finding it cost effective to transport empty containers back from the USA in an attempt to meet container demand in Asia. Unfortunately, this additional cost of return shipping is also being passed further down the chain, adding fuel to the fire.
While there is some evidence that global shipping prices have peaked (indeed, CMA, one of Europe’s largest shipping companies, has put a cap on their spot prices going into 2022 – an act of goodwill it would seem(3)), it is important to note that as COVID-19 restrictions start to subside, global trade volume will continue its upward trend. A further disruption or worsening of port congestions is all it would take for the rates to hike again.
Fuel Costs
A little-discussed matter, overshadowed by COVID-19, that has had a significant impact on shipping costs from January 2020 until today, is the tighter Sulphur content restrictions in marine fuels. New regulations, referred to informally as IMO 2020, reduce the maximum permitted percentage of Sulphur in fuel from 3.5% to 0.5%. According to an analysis by BCG, this will lead to an increase of $25 billion to $30 billion in fuel costs for container liners by 2023(7). While liners can share the costs of environmentally friendly services with their customers and promote the social responsibility of greener supply chains, the additional cost burden is magnified by the impact of COVID-19 and passed down the supply chain.
It will be years or even decades before technology catches up to manage such instances (as the current strain on the global supply chain). It is where waves become ripples before finally, things run as smoothly as possible.”
– James Chen, Kordz Managing Director
Material & Labour Costs
Due to the globalization of the world economy, it has become increasingly difficult to isolate the cost of goods and raw materials from the rising cost of global shipping. Most trade is priced in quickly depreciating US dollars, despite predictions that the value will rise by the end of 2021. From a US dollar perspective, the price of raw materials has been increasing, as many raw material producing countries have been experiencing a lack of workers at the coalface due to the COVID-19, resulting in supply-side shocks.
China’s rising labour cost over the past year are a continuation of the trend of rising wages in the country over the past couple of decades. A significant proportion of wage growth is attributed to increases in minimum wages, which are set every couple of years by various provinces by taking into account both the regular rate of growth as well as current market conditions. Since 2010, approximate wage expense in Chinese manufacturing has more than doubled(2).
In addition, as China’s population continues to transition to a service-based economy, the pool of unskilled workers is diminishing, particularly in coastal regions with greater population density(4).
Copper: Limited Supply, Spiked Demand
“Copper prices rise and fall all the time. Shipping costs and shipping times have also. What is unprecedented, is those two factors increasing simultaneously with the demand for products, coupled with the COVID-19 challenges with the addition of tariffs. This has really presented a momentous business challenge for factories, distributors, and integrators.”
– Eric Bodley, Kordz Partner USA, Future Ready Solutions

Copper is a prime input material valued in almost every industry and it is 100% recyclable; however, its increasing popularity has been particularly seen in the utilities (mostly renewables), and the electrical vehicle industries. Increased Work From Home (WFH) demands on communications electronics and regulatory bodies enforcing environmental sustainability are creating higher demand for copper in unprecedented amounts.
In March 2021, China’s imports of copper increased by 25% compared with March 2020, making it one of the world’s largest consumers of metal. Global supply shortages (potentially due to shipping delays), as well as a falling US Dollar, has seen copper prices rocket to new heights, from lows of US$4,600/tonne in March 2020 to around US$10,000 as of this writing. Since the beginning of the year, China has released some 30,000 tonnes of copper from strategic reserves in order to stabilize market prices(6).
On a more positive note, in spite of the challenges faced by COVID-19, global copper production remained flat in 2020 compared with 2019. As copper demand increases, so too has copper production potential, as the elevated prices incentivise miners to open new mines. The International Copper Study Group (ICSG), an organisation representing the interests of both copper producers and consumers, predicts that global refined copper production will increase by about 3% in both 2021 and 2022(5). However, it is worth noting that while these will support the increased demand for copper, the supply alleviation of significant mining operations will take upwards of five years.
The market trends currently seen in the global copper market are indicative of the market trends in the majority of other input materials, such as plastics, paper, wood and even steel and aluminium. As demand continues to increase in the post-pandemic era, so too will challenges facing the global commodities market.
The Impact on Manufacturing Times and Procurement
In the past, international shipping from Hong Kong to Europe took on average of 45 days door-to-door. With the recent strain on the logistics channel it can take anywhere up to 90 days, with plenty of anecdotal tales of much longer delays around the world.
Shortages in input components and raw materials in the manufacturing hubs of the world add further volatility to the supply chain, as competition for raw material availability and in some cases forced furloughs have occurred as a matter of survival. This has caused greater supply chain volatility and caused most companies to hold more inventory as a proportion of sales. Due to the increased demand, the already overburdened supply chain is further strained, and longer delays have been caused.
We have been observing a reduction in factory activity since September, due partly to the power restrictions and shortages across the manufacturing hubs of China, which indicates a reduction in supply in the coming months. However, some observers are forecasting a reduction of supply chain volatility by Q2 of 2022, once the increased demand from COVID-19 WFH policies subside and container shortages are resolved.
“We have recently seen a shift in the supply chain where integrators are now realising that they need to stockpile some essential products to meet demand, since distributors can no longer plan for on time deliveries.”
– Eric Bodley, Kordz Partner USA, Future Ready Solutions
When supply access hits a bottleneck, it is basic human nature to stockpile. In the pre-COVID-19 world, we were afforded the luxury of picking and choosing what products to stockpile and when. However, saving for a rainy day has no longer become an option. The struggling supply chain and production delays has forced suppliers’ hand with seemingly every day being a rainy day. The adjustments needed for AV professionals are pivotal and can shape the way the industry does business now and in the future, even after the supply chain issues are resolved.
How to adjust as an AV professional
“The opportunity here is for us to do a better job of forecasting and ordering, and not rely on the typical shipping times we have seen in the past, and to expect shipping delays to continue for the foreseeable future.”
– Eric Bodley, Kordz Partner USA, Future Ready Solutions
Every cloud has silver lining, and of course, despite the challenges, opportunities still abound for AV professionals to adjust and navigate these choppier waters until things calm down once again.
To begin, we need excellent communication. AV Distributors must continue to work closely with their suppliers to stay realistic about demand, shipping times, and work toward keeping products in stock at higher levels to counteract the ups and downs of supply. Downstream communication and transparency to inform customers of supply issues are integral to maintaining stability. This means alerting customers ahead of time to opportunities and potential risks to supply. In this environment, distributors can add value and protect their business and those of their customers with a good working knowledge of how to cost effectively substitute products with another variation or next-step-up to quickly solve any supply problems and keep the wheels turning.
Next, we need to maintain good stock levels. Where possible, it’s important to stock products that are in demand right now. Equally important is to stay ahead of the curve and stock the products that are emerging as the new standard for tomorrow. With the way the global pandemic is changing our lives, technology is advancing at an accelerated rate to acclimate us to the “new normal”, and with it comes the need for higher-performing products and the connectivity that make it all possible.
Prioritise Products Now
Consumers using home networks are driving unprecedented demand for residential integrators’ products and services. Increased bandwidth available to the home, as well as fibre optic cabling being deployed directly to the home, has contributed to the sales of networking cables, fibre optic cabling, and the installation of increasingly more products in the home by residential integrators. While the supply chain and manufacturing outputs are volatile, it pays to forecast the products needed not just for the near future of yourself and clients, but for the advancements in technology becoming more widely available and accepted.
No more ‘just-in-time’ installations
With a strained supply chain and increased demand at the consumer level, the era of just-in-time supply meeting spontaneous integrator demand is gone. Production on the basis of unstable logistics markets and a trickle-down effect in the volatile supply chain means supply for integration projects needs to be well planned well ahead of expected project commencement.
Integrators and distributors need to optimise for the logistics of volatile and inefficient supply, accounting for worst-case-scenario with higher cost, prolonged lead time and room for possible delays. This will ensure a level of business transparency, continuity and stability. Integrators should prepare designs and preliminary work as soon as possible, even when they’re not ready to order so that when product is available it can begin at a moment’s notice.
Today’s Stock is Tomorrow’s Profit
Lastly, contrary to popular belief, ballooning shipping and material costs can be an opportunity for integrators. Ongoing price inflation will ensure what you bought yesterday can be worth more tomorrow. In the longer term, purchasing supplies earlier in the cycle will result in better margins when brands increase their prices. Those who order when there’s inventory available will have a better chance of success with winning or delivering their projects. To do so, integrators must have open lines of communication with their suppliers with a greater lead time for projects. There’s never a ‘too early’. AV professionals who get confirmation on projects and order inventory early will have greater success and profitability with projects. In short, AV professionals must stay in touch with distributors with plans to order when there’s availability. Distributors must stay in contact with AV professionals to forecast demand in real-time.
Be prepared for extended lead times on projects. Counterintuitively, AV professionals must charge accordingly for these delays. If projects are designed for reliability and engineered for use rather than cutting edge, there should be less fear of redundancy.
Again, work with distributors to make realistic forecasts of availability and make realistic promises with the standard of products that the client deserves.
Summary
The disruptions in the global supply chain have demonstrated just how thin the global shipping infrastructure was prior to the pandemic and how much is needed to make this system robust. Stable global logistics is becoming as much an essential utility now as electricity or communication and there are huge investment requirements in this sector to support the infrastructure back to normalisation and then growth.
Supply and demand forces in logistics and manufacturing will eventually balance out. In the interim, suppliers and integrators who plan what product to prioritise and when will outperform those who fail to plan accordingly. As the world transitions to Work from Anywhere, the demand on consumer electronics and its associated installation has created new demand for the AV professional. This is an opportunity for the AV professional to keep open lines of communication with their customers – whether they be suppliers, integrators, or end users.
Forecasting an uncertain future takes collaboration. While we can’t be certain of what the near-future holds, we are certain that open lines of communication and joint planning for uncertainty can see us through.
Resources
- ABC News., Worldwide shipping costs skyrocketing as system descends into crisis | The World
- https://tradingeconomics.com/china/wages-in-manufacturing
- Drewry https://www.drewry.co.uk/supply-chain-advisors/supply-chain- expertise/world-container-index-assessed-by-drewry
- China Briefing – A Guide to Minimum Wages in China in 2021
- International Copper Study Group (ICSG) https://www.icsg.org/index.php/press-releases/finish/113-forecast-press- release/3098-2021-05-03-icsg-forecast-press-release
- China to release more metal reserves – Xinhua News http://www.news.cn/english/2021-09/27/c_1310212962.htm
- https://www.bcg.com/publications/2019/sharing-costs-imo-2020-across-ecosystem